1966
First Lube Refinery
The construction work of first Lube Refinery was started in May 1964. The Refinery came into production in June 1966,
with crude oil refining capacity of 539,700 tons per annum and production of 76,000 tons of various grades of Lube Base Oils
and 100,000 tons of Asphalt per annum. This Refinery also supplemented fuel products requirement of the country particularly
Kerosene and Diesel.
1972
On January 16, 1972, the Government of Pakistan took over the management of the Refinery under the Economic Reforms Order.
The overall managerial directions were entrusted to the Ministry of Production.
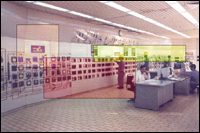
1977
Fuel Refinery
The growth in demand of fuel products in the subsequent years,
after installation of first Lube Refinery, impelled the need for further increase in refining capacity.
In the year 1974, National Refinery Limited signed an agreement with Industrial Export and Import of
Romania to construct a Fuel Refinery having crude refining capacity of 1.5 million tons per year on turnkey basis.
Since the Fuel Refinery was to be integrated with the first Lube Refinery, a site on the same premises was selected.
NRL's Fuel Refinery was a fresh addition on the country's growing industrial landscape.
The Fuel Refinery was commissioned in 1977 for producing LPG, Motor Gasoline, HOBC, Naphtha, Kerosene,
Jet Fuels (JP-l), (JP-4), High Speed Diesel Oil (HSD), Furnace Oil.
1979
BTX Plant
In order to meet country's demand of petrochemicals/solvents Benzene,
Toluene and Xylene, particularly Toluene, to meet Defense requirements,
installation of a BTX plant was seen feasible. Feedstock to BTX plant was also available from the Fuel Refinery.
A Petrochemical BTX plant was therefore installed in 1979, which was capable of producing 25,000 Metric tons per Annum of Benzene,
Toluene and Xylene.
The country's first petrochemicals unit was integrated with the units of the Fuel Refinery. Currently it is out of operation.
1980
Propane Recovery Unit (PRU)
In order to meet high purity Propane requirement for extraction and refrigeration
at various units of Lube Refinery, a Propane Recovery Unit was installed and commissioned in 1980.
Detailed engineering and fabrication for the entire plant was done locally.
The plant is designed to produce 1,200 tons per annum of high purity Propane,
which meets the requirement of both Lube Refineries.
1985
Second Lube Refinery
In early 1980's the industrial growth in Pakistan changed the petroleum products supply demand scenario.
Fuel business was saturating whereas there was a captive market of lube oils in the region.
In view of this, NRL installed its second Lube Refinery, which was commissioned in 1985 for producing 100,000 tons of Lube Base Oils.
The feedstock for this Lube Refinery was available as surplus Furnace Oil from Fuel Refinery, which was upgraded to Lubes.
Basic engineering and design work for this project was carried out by CE Lummus of U.K under
consultation with Taxaco Development Corporation of USA As a result of concerted efforts,
a refinery representing the latest technology appeared in the highly impressive NRL Complex.
The completion of second Lube Refinery created the largest and the most comprehensive crude oil
refining complex in the country.
1990
Fuel Refinery Revamp
Demand of fuel products in the country had positive growth rates in the late eighties.
However, the cost effectiveness of the projects gained prior importance.
Thus, in order to keep-up the pace with modern refineries and to reduce the processing cost per barrel of crude,
NRL implemented its Fuel Refinery Revamp Project in 1990. The revamp project was based on Energy Conservation,
enabling the capacity increase by 15,000 BPSD without increasing energy consumption. After the revamp,
the total crude processing capacity of NRL was enhanced to about 2.71 million tons per year.
The balancing and modernization of platforming unit was undertaken in 1995 and installation of larger sized reactors in 1997.
Increased production of High Octane reformat by 70%, gave potential for production of high quality, unleaded motor gasoline.
1998
The corporate control of National Refinery was transferred to the Ministry of Petroleum & Natural Resources.
2000
Self Power Generation
Based on the principle of cogeneration from high-pressure steam boiler,
a 7.5 MW power generation unit has been installed to decrease dependence on purchased power supply.
With the commissioning in year 2000, beside energy conservation and supplying low cost electricity,
the Self Power Generation is helping in reducing production losses due to interruption in power supply.
2005
Lube II Refinery Dewaxing Unit Revamp Project
In order to meet the growing demand of LBO, a Lube Revamp Project was undertaken with the Technical Assistance
of Exxon Mobil in year 2005. On completion of the Project, the production capacity of the second Lube Refinery
was enhanced by 14,800 TPA. Dilchill Crystallization Process Technology was utilized for production of High
Viscosity Bright Stock (BS HVI) grade of Lube Oil.
2012
Product Metering System
Company has implemented Product Metering System at refinery and Keamari Terminal for custody transfer of product to Oil Marketing Companies (OMCs). Initially project is handling HSD pumping to OMCs.
Radar Gauging System
Radar Gauging System for accurate measurement of tanks for custody transfer has been installed on 105 tanks.
2015
Information Technology
The company has a strong information technology capability. Computerized instrumentation and auto-tank gauging are being applied. The technical staff uses a variety of computer software for process design, performance monitoring, simulation and engineering design.
NRL had implemented an Enterprise Resource Planning (ERP) solution, SAP(version 4.6C) in the year 2004 with following modules:
- · Finance and Controlling (FICO)
- · Material Management (MM)
- · Sales & Distribution (SD)
- · Plant Maintenance (PM)
- · Human Resource (HR)
During 2015-16, the Company has successfully up-graded its ERP system to ECC6, the last available SAP version, for improved Management and Financial Reporting, with some added features and following additional modules:
- · Projects Systems (PS)
- · Audit Information Systems (AIS)
- · Quality Assurance (QA)
2017
CDU Revamp Project
The Company has successfully completed the revamp of crude distillation column in April 2017. As a result, the crude oil processing capacity has been enhanced by 3000 barrels per day increasing the overall designed capacity from 62,000 barrels per day to 65,000 barrels per day.
DIESEL DESULPHURIZATION
In line with the direction of Ministry of Petroleum and Natural Resources to achieve Euro-II standard HSD (less than 500 ppm) NRL successfully implemented the project of Diesel desulphurization (DHDS). The plant has a capacity to reduce sulphur to as low as 10 ppm which may help NRL to meet future requirements. The project was successfully commissioned in June 2017. The project cost of DHDS incurred by the company is Rs.26 billion, without any major increase in revenues as the incentive initially announced by the Government for increasing the deemed duty from 7.5% to 9% has been delayed. The company is in discussion with GoP to allow refineries increase in deemed duty so that the huge investment cost and processing cost could be recovered.
ISOMERIZATION
Isomerization project started two years ago has been successfully commissioned in October’ 2017. Through Isomerization company would succeed in converting majority of its Naphtha, which has no local market, to Motor Gasoline which would meet the Country’s requirements as well as result in fetching higher price. Total isomerate production capacity of NRL is 6,793 BPSD.
2020
Two stage unit revamp at Lube-I refinery
The project has been commissioned in September 2020 and it has enhanced the installed crude oil processing capacity of Lube-I refinery from 12,050 Barrel per stream day (bpsd) to 17,000 bpsd and vacuum fractionation capacity from 5,200 bpsd to 6,600 bpsd.
2021
Production and Supply of Euro-V High Speed Diesel (HSD)
Effective January 01, 2021 NRL has started to supply HSD compliant with Euro-V specifications, as provided by the Ministry of Energy (Petroleum Division), from its DHDS upgradation plants which were commissioned in June 2017.